Safeguard your machinery's longevity with these crucial lubrication methods: select the appropriate lubricant, uphold proper frequency, monitor levels, apply correctly, prevent over-lubrication, avoid under-lubrication, and conduct regular maintenance checks. These practices optimize efficiency, minimize wear, and prevent untimely breakdowns, assisting in peak performance and cost reduction.
Proper Lubricant Selection
When selecting lubricants for machinery, always prioritize factors like viscosity, additives, and compatibility to guarantee peak performance.
Viscosity is an important aspect to think about as it directly impacts the lubricant's ability to protect and reduce friction between moving components. The right viscosity ensures that the lubricant flows effectively to all necessary areas within the machinery.
Additionally, additives play a key role in enhancing performance, especially in demanding conditions, by preventing wear and corrosion.
Ensuring compatibility with machine materials is essential to prevent premature wear, breakdowns, and potential equipment damage.
Opting for reputable brands that adhere to industry standards is essential for reliable lubricant selection, ensuring that your machinery operates at its best.
Making informed choices about lubricants based on these factors will contribute significantly to the excellent performance and longevity of your machinery.
Adequate Lubrication Frequency
To guarantee peak performance and longevity of your machinery, maintaining an appropriate lubrication frequency is vital. Adequate lubrication frequency is essential to secure maximum protection against premature component failure. The ideal lubrication frequency varies depending on factors such as operating conditions, load levels, and temperature changes. Following regular lubrication intervals as recommended by the manufacturer is key to preventing friction, wear, and unexpected breakdowns.
Both over-lubrication and under-lubrication can have negative consequences on your machinery. Over-lubrication may lead to overheating and excess oil consumption, while under-lubrication can cause increased friction and accelerated wear on components. Monitoring equipment performance and lubricant condition can guide adjustments to the lubrication frequency, helping you achieve the best balance for machinery longevity.
Monitoring Lubricant Levels
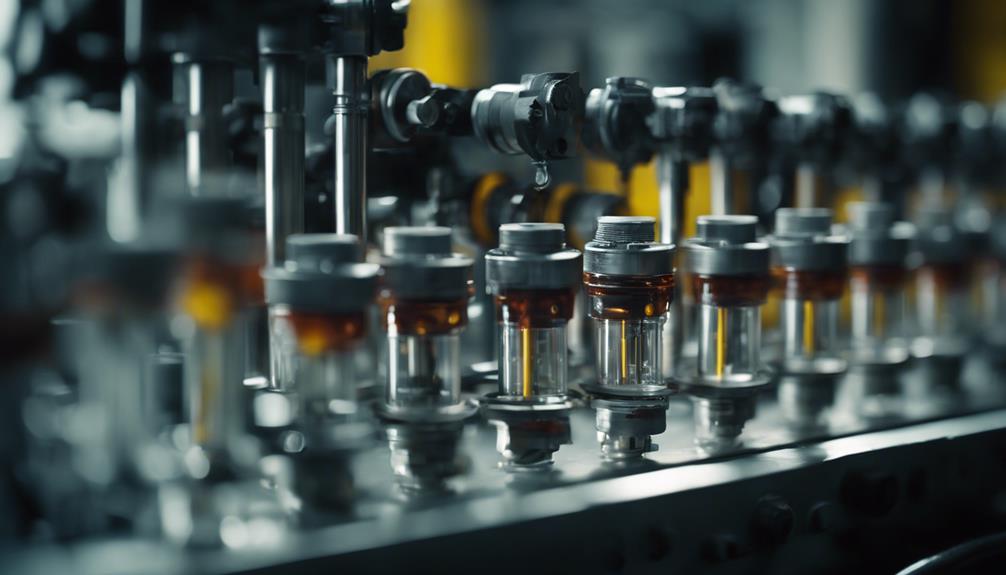
You need to regularly check the lubricant levels in your machinery to guarantee it functions at its best. Utilize monitoring tools and consider implementing automated systems for efficient maintenance.
Monitoring lubricant levels is essential in preventing wear, friction, and potential equipment failures.
Regular Level Checks
Consistently monitoring lubricant levels is essential for ensuring peak equipment performance and longevity. Proper lubrication levels are vital for preventing breakdowns, reducing friction, heat buildup, and wear on machinery components. By regularly checking levels, you can detect leaks, overfilling, or contamination that may jeopardize equipment operation.
Maintaining the correct lubricant levels not only enhances peak equipment performance but also promotes efficient energy consumption, ultimately leading to reduced maintenance costs. Regular level checks play a significant role in equipment maintenance, extending the equipment lifespan, and safeguarding against unexpected breakdowns.
Make it a routine to monitor lubricant levels diligently to keep your machinery running smoothly and effectively.
Utilize Monitoring Tools
Monitoring tools play a crucial role in maintaining ideal lubricant levels and preventing equipment damage. By utilizing these tools, you can gather data on lubricant usage patterns, allowing for efficient scheduling of timely refills. This proactive approach helps in reducing friction, heat, and wear on machinery components, ultimately extending their lifespan.
Regularly checking lubricant levels enables you to detect potential leaks or excessive consumption early on, preventing costly damages down the line. Monitoring lubricant levels not only guarantees top performance but also serves as a cost-effective method to avoid unexpected breakdowns.
Stay ahead of maintenance by integrating monitoring tools into your lubrication practices for long-term equipment health.
Implement Automated Systems
Implementing automated systems for monitoring lubricant levels guarantees continuous maintenance of ideal levels necessary for efficient machinery operation. These systems ensure that lubricant levels are consistently at best levels, preventing equipment damage due to insufficient lubrication.
By alerting maintenance teams when levels are low, automated systems reduce the risk of human error in checking and refilling lubricants, thereby improving overall equipment reliability. Real-time data provided by these systems allows for proactive maintenance scheduling based on actual lubricant usage patterns, enhancing machinery operation.
Additionally, automated monitoring systems can integrate with maintenance software for streamlined lubrication management, ultimately contributing to improved equipment longevity. Embracing automated systems for monitoring lubricant levels is a proactive step towards ensuring the longevity and efficiency of your machinery.
Correct Lubricant Application Techniques
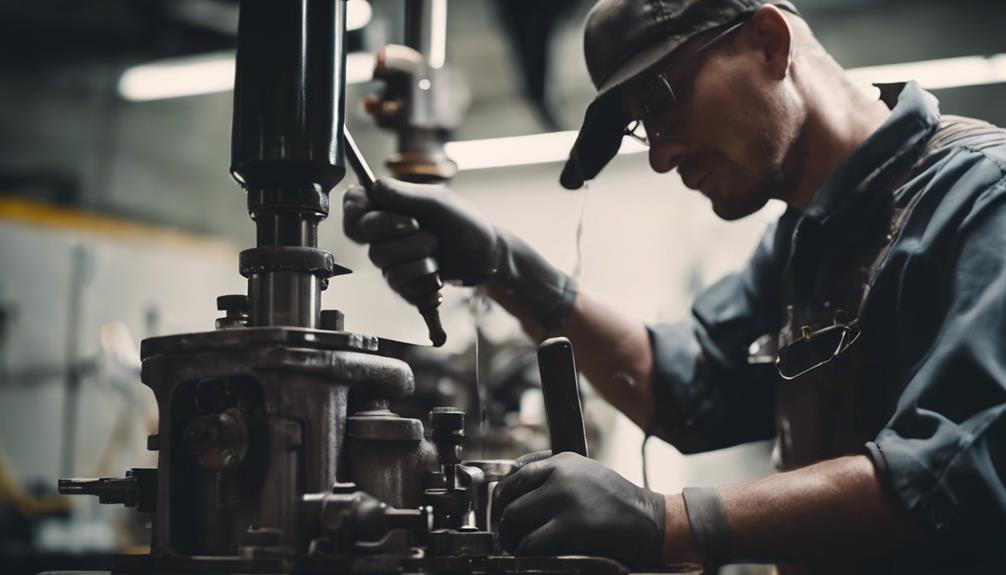
When it comes to machinery lubrication, using the correct lubricant application techniques is essential. Ensuring you select the right lubricant and applying it effectively in the appropriate areas can greatly impact the performance and lifespan of your equipment.
Proper Lubricant Selection
Considering factors like viscosity, additives, and compatibility with machine materials is essential when selecting the right lubricant for peak machinery performance. Choosing the proper lubricant helps prevent increased friction, wear, and potential equipment failure.
The correct lubricant application techniques guarantee ideal coverage and effectiveness in reducing friction. Applying the right amount of lubricant is vital to prevent excess buildup that can attract contaminants and hinder machinery performance.
By regularly monitoring and adjusting lubricant application methods, you can maintain equipment longevity and efficiency. Make informed decisions based on the specific requirements of your machinery to avoid issues caused by using the wrong lubricant.
Prioritize the longevity and performance of your equipment by selecting and applying lubricants correctly.
Effective Application Methods
To guarantee peak performance and longevity of your machinery, mastering correct lubricant application techniques is essential. Proper lubricant application involves using the right amount of lubricant at the correct intervals to maintain consistent lubrication levels and prevent excessive wear on moving parts.
It's vital to confirm uniform coverage of the lubricant on all necessary components for smooth operation. Over-lubrication can lead to inefficiencies and potential damage, while under-lubrication may cause increased friction and premature wear and tear.
Utilizing appropriate tools and equipment, such as oilers or grease guns, for lubricant application can enhance accuracy and efficiency in maintenance practices. Remember, choosing the correct lubricant type is just as important as the method of application for the efficient functioning of your equipment.
Preventing Over-Lubrication
To prevent over-lubrication in machinery, make sure that lubricant levels are monitored regularly and follow manufacturer recommendations. Over-lubrication can lead to higher operating temperatures, increased energy consumption, and premature equipment failure.
Excessive lubricant quantities can cause leaks, contamination, and reduced system efficiency. By monitoring lubricant levels and adhering to manufacturer recommendations, you can avoid these issues. Utilizing automatic lubrication systems can help maintain precise lubricant amounts, preventing over-lubrication.
Proper training of maintenance personnel on lubrication practices is vital in reducing the risk of over-lubricating equipment. This training ensures that individuals understand the importance of following guidelines to prevent over-lubrication and its negative consequences.
Avoiding Under-Lubrication
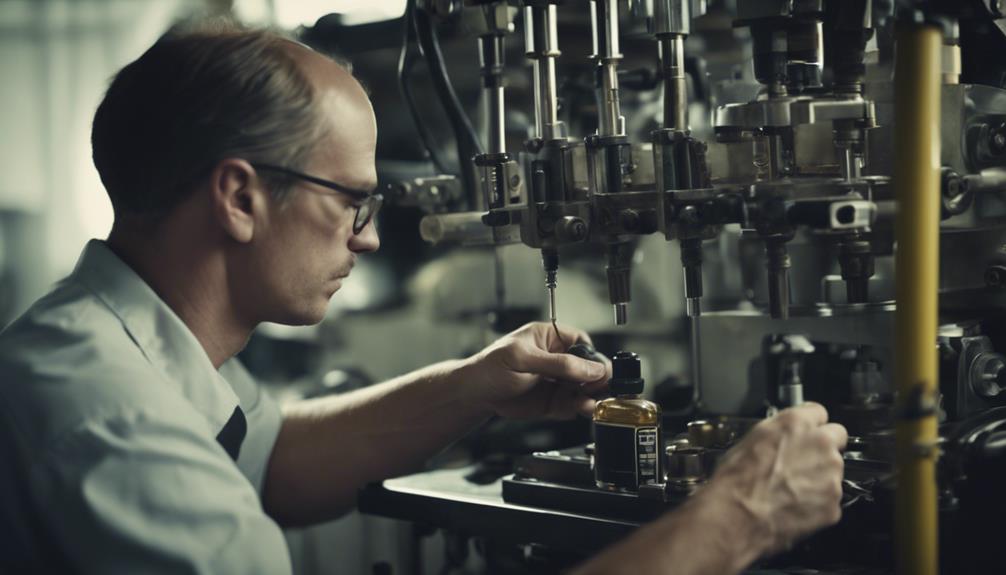
Regular monitoring of lubricant levels is vital to prevent under-lubrication issues in machinery components, promoting peak performance and longevity. Under-lubrication can lead to increased friction, wear, and heat generation, compromising the equipment's efficiency and lifespan.
To avoid these detrimental effects, it's essential to monitor lubricant levels regularly and guarantee proper lubrication. Inadequate lubrication not only accelerates wear and tear but also generates excess heat, potentially causing unexpected breakdowns and costly repairs.
By following the manufacturer's recommendations for lubrication intervals and quantities, you can prevent under-lubrication issues and maintain excellent machinery function. Proper lubrication not only minimizes downtime but also enhances equipment performance, ultimately extending its lifespan.
Stay proactive in monitoring lubricant levels to keep your machinery running smoothly and efficiently for years to come.
Implementing Regular Maintenance Checks
Monitoring lubricant levels through regular maintenance checks is key to identifying and addressing any potential issues that could lead to equipment breakdowns. Scheduled inspections help monitor lubricant levels, identify wear and tear, and maintain peak equipment performance.
By implementing routine maintenance practices, you enhance machinery reliability and minimize unexpected downtime. Consistent checks for lubrication quality and quantity help extend equipment lifespan and improve operational efficiency.
Timely maintenance checks allow for proactive maintenance actions, reducing the risk of costly repairs and replacements. Make sure to prioritize implementing regular maintenance checks to guarantee that your machinery operates at its best and lasts longer.
Conclusion
By following these 7 essential machinery lubrication methods, you'll guarantee your equipment runs smoothly for years to come.
Neglecting proper lubrication is like driving a car without oil – a disaster waiting to happen!
So, don't risk costly repairs and downtime.
Stay on top of your lubrication game and watch your machinery thrive!